- Service Manual Honda
- Caterpillar G3304 Service Manual Transmissions
- Bike Service Manual
- Caterpillar G3304 Service Manuals
PDF Service Manuals, Operation & Maintenance Manuals, Spare Parts Catalogs. Contact / About. Write and Ask brovertek@gmail.com. CAT G3304 Gas diesel engine: 152711 1RG G3304 GAS ENGINE-INDUSTRIAL 152712 37Y G3304 GAS ENGINE-INDUSTRIAL 152713 N4F G3304. Caterpillar 301.8c caterpillar 301.6c caterpillar 301.8c caterpillar 302.5c caterpillar 303.5c cr caterpillar 303c cr caterpillar 304c cr caterpillar 305c cr.
Usage:
G330607YService Manual Honda
Magneto
Tools Needed | Quantity | |
9U-6958 | Magneto Test Module | 1 |
The following components of the instrument panel can affect the output of the magneto: magnetic switch, stop switch, engine oil pressure gauge and water temperature gauge. Determine if the components are working properly. There may be a problem with an overspeed contactor or an activated overspeed contactor rather than the magneto. Also, make sure that the gas shutoff valve is OK.
Use the 9U-6958 Magneto Test Module for measuring the voltage that is supplied to the spark plug by the magneto. The Operating Manual, NEHS0588 is provided with the tool.
Bench testing of the magneto is performed by the manufacturer.
Ignition Timing
- Determine the correct ignition timing for the fuel.
- Obtain a fuel analysis.
- Enter the data from the fuel analysis into the Caterpillar Software Program, LEKQ6378, 'Methane Number Program'.
- Refer to Engine Performance, LEBH9529, 'G3300 Industrial', 'Fuel Usage Guide' or Engine Performance, LEBX9532, 'G3300 Generator Set', 'Fuel Usage Guide' or consult with your Caterpillar dealer in order to determine the desired ignition timing.
Timing of Magneto to Engine (Solid State Altronic)
Tools Needed | Quantity | |
9U-5358 | Timing Light Gp | 1 |
- Turn the crankshaft in the direction of engine rotation until the No. 1 piston is coming up on the compression stroke. Refer to Testing and Adjusting, 'Finding Top Center Position for No. 1 Piston'. Also observe the direction that the pointer on the magneto moves.
Note: The magneto has two marks that indicate the rotation of the magneto ('CW' and 'CCW'). The magneto also has a pointer that moves clockwise or counterclockwise when the crankshaft is rotated. When you time the magneto to the engine, the pointer must indicate the correct timing mark.
Illustration 1 g00743172 Marks for the direction of rotation and pointer on the magneto Show/hide tableIllustration 2 g00735090 Flywheel timing marks - Observe the timing marks on the flywheel. Turn the crankshaft until the desired timing mark on the flywheel is directly under the pointer for the timing marks on the flywheel.
- Observe the pointer on the magneto.
When the desired timing mark on the flywheel is obtained, the pointer on the magneto must be aligned with the appropriate mark.
If the pointer on the magneto is not aligned with the appropriate mark, remove the magneto from the engine.
- Align the pointer on the magneto with the appropriate mark for the direction of rotation.
Illustration 3 g00743728 Lugs on the magneto drive tang - Pull the magneto drive away from the magneto drive housing. Align the slots of the magneto drive with the lugs on the magneto drive tang. Push the magneto drive back into the housing.
- Keep the pointer on the magneto aligned with the appropriate mark and install the magneto.
- Align the pointer on the magneto with the appropriate mark for the direction of rotation.
- Start the engine. Operate the engine at high idle speed.
Note: Do not adjust the timing at low idle because of the timing advance in the magneto.
- Attach a timing light to the secondary lead for the spark plug of the number 1 cylinder. Use the timing light to observe the timing marks on the flywheel. If necessary, loosen the bolts for the magneto and rotate the magneto in order to gain the desired timing. When the timing is correct, tighten the bolts for the magneto.
- Install the covers for the flywheel housing.
Solid State Altronic Canadial Standards Association (CSA) and ATEX Applications
The ignition harnesses for engines in potentially explosive atmospheres are protected by thick braided covers. The ignition pulses in the harnesses might not be detected by many timing lights because of the braided covers.
A fabricated jumper cable will enable the timing light to detect ignition pulses. The fabricated cable is installed between the ignition harness connector and the ignition transformer of the number 1 cylinder.
Tools Needed | Quantity | |
Fabricated jumper cable | 1 | |
Description | Part No. | |
Amphenol three-pin connector | MS3101A-10SL-3P | 1 |
Amphenol three-socket connector | MS3101A-10SL-3S | 1 |
16 AWG Red wire | Approximately | 1 |
16 AWG Black wire | Approximately | 1 |
16 AWG Green wire | Approximately | 1 |

- Assemble the materials listed in Table 2 according to the Illustration 4 schematic. Show/hide table
Do not disconnect equipment unless power has been disconnected or the area is known to be non-hazardous
- Disconnect the ignition harness from the number 1 cylinder. Connect the fabricated jumper harness between the ignition number 1 cylinder connector and the number 1 cylinder ignition transformer.
- Follow the procedure that is described above in 'Timing of Magneto to Engine (Solid State Altronic)'. When you perform the procedure, attach the timing light to the wiring for the fabricated jumper cable.
- After the procedure is completed, stop the engine. Remove the fabricated jumper cable. Reconnect the ignition harness to the ignition transformer for the number 1 cylinder.
Illustration 4 | g02725233 |
(1) Three-pin connector (2) Three-socket connector |
Timing of Magneto to Engine (Solid State Fairbanks Morse)
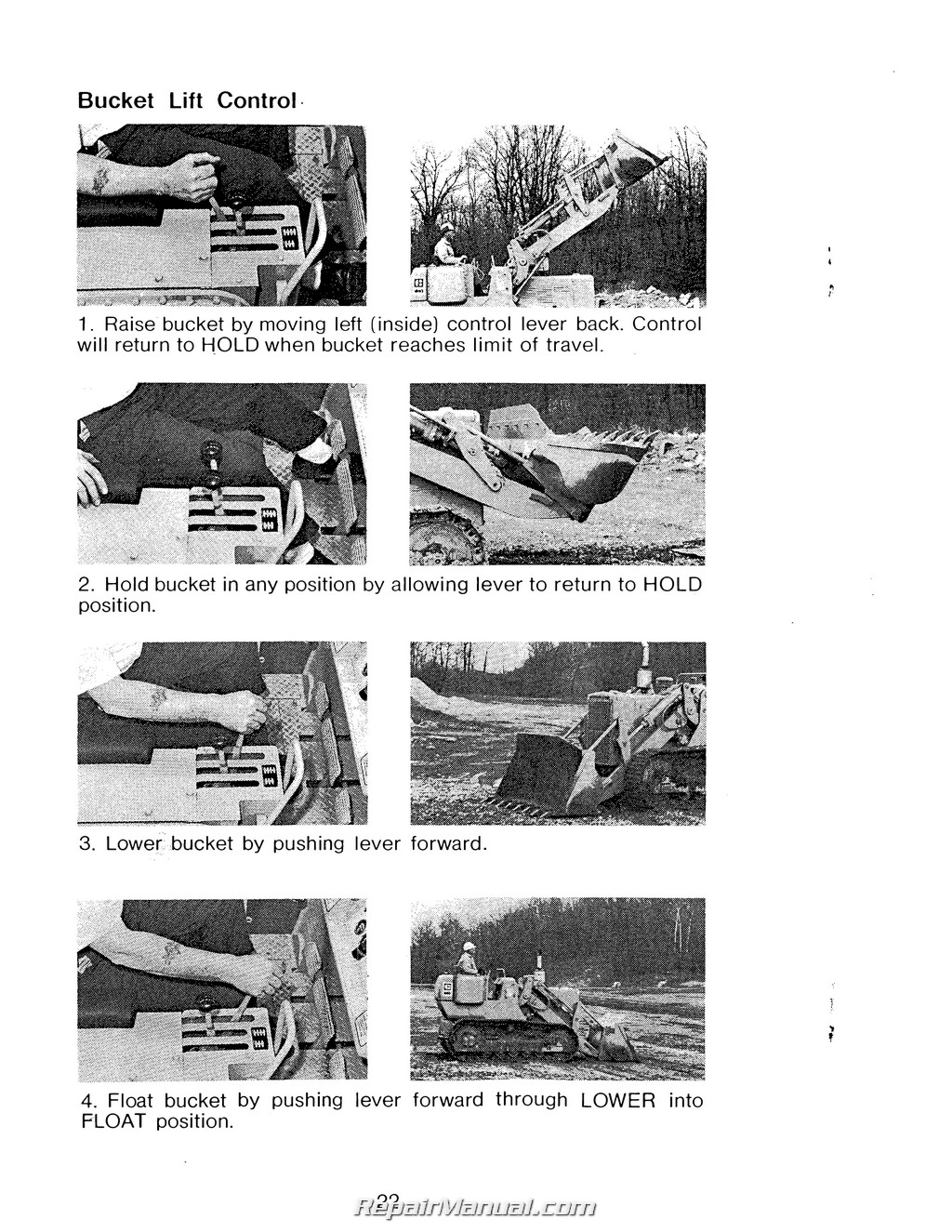
Tools Needed | Quantity | |
9U-5358 | Timing Light Gp | 1 |
- Turn the crankshaft in the direction of engine rotation until the No. 1 piston is coming up on the compression stroke. Refer to Testing and Adjusting, 'Finding Top Center Position for No. 1 Piston'. Show/hide table
Illustration 5 g00735090 Flywheel timing marks - Observe the timing marks on the flywheel. Turn the crankshaft until the desired timing mark on the flywheel is directly under the pointer for the timing marks on the flywheel.
- Remove the magneto from the engine.
Illustration 6 g00812376 (1) Timing bolt - Remove timing bolt (1) and turn magneto drive until the yellow mark on the gear is in the center of the hole. Show/hide table
Illustration 7 g00814081 G3304 Engine magneto
(1) 30 degree angle of the drive coupling from the vertical positionIllustration 8 g00814077 G3306 Engine magneto
(1) 45 degree angle of the drive coupling from the vertical position - Place the magneto drive coupling in the proper position. To rotate the drive coupling, pull out the coupling and rotate the coupling to the correct position. When the coupling is in the correct position, push in the coupling in order to engage the gear teeth.
- Install the magneto in order to engage the drive tang and the drive slot.
- Start the engine. Operate the engine at high idle speed.
Note: Do not adjust the timing at low idle because of the timing advance in the magneto.
- Attach a timing light to the secondary lead for the spark plug of the number 1 cylinder. Use the timing light to observe the timing marks on the flywheel. If necessary, loosen the bolts for the magneto and rotate the magneto in order to gain the desired timing. When the timing is correct, tighten the bolts for the magneto.
Timing of the Spark Gap Magneto to the Engine
Tools Needed | Quantity | |
9U-5358 | Timing Light Gp | 1 |

- Turn the flywheel in direction of engine rotation until the No. 1 piston is coming up on the compression stroke. Refer to Testing and Adjusting, 'Finding Top Center Position for No. 1 Piston'.
Illustration 9 g00735090 Flywheel timing marks - Observe the timing marks on the flywheel. Turn the crankshaft until the desired timing mark on the flywheel is directly under the pointer for the timing marks on the flywheel.
- Remove the magneto from the engine. Show/hide table
Illustration 10 g00812380 Position of the magneto drive
(1) Timing bolt
(2) Drive coupling and drive slot - Remove timing bolt (1). Turn the magneto drive in order to position the yellow mark that is on the distributor disc in the center of the hole. Install the timing bolt.
- Place drive coupling (2) in the vertical position. To rotate the drive coupling, pull out the coupling and rotate the coupling. When the coupling is in the correct position, push in the coupling in order to engage the gear teeth.
- Install the magneto in order to engage the drive tang and the drive slot.
- Start the engine. Operate the engine at high idle speed.
Note: Do not adjust the timing at low idle because of the timing advance in the magneto.
- Attach a timing light to the secondary lead for the spark plug of the number 1 cylinder. Use the timing light to observe the timing marks on the flywheel. If necessary, loosen the bolts for the magneto and rotate the magneto in order to gain the desired timing. When the timing is correct, tighten the bolts for the magneto.
- Install the covers for the flywheel housing.
Adjustment of the Brush Spring
Illustration 11 | g00812377 |
(1) End cap assembly (2) Gasket for end cap assembly (3) Distributor block (4) Dowel rod (5) Distributor disc (6) Brush and spring assembly |
Measure the distance between distributor block (3) and the face of the distributor disc (5). The correct clearance indicates the correct pressure on the brush and spring assembly (6).
- Remove the timing bolt and install dowel rod (4) between distributor block (3) and distributor disc (5). The correct clearance is
3.96 to 5.56 mm (0.156 to 0.219 inch) . - To increase the clearance, add additional gaskets (2) for the end cap assembly. To reduce the clearance, add number 10 washers between distributor block (3) and end cap assembly (1).

Ignition Transformers
Check the transformer resistance. Refer to Specifications, 'Transformer'.
Spark Plugs and Adapters
Caterpillar G3304 Service Manual Transmissions
Tools Needed | Quantity | |
1F-0479 | Wrench | 1 |
9U-6695 | Spark Plug Firing Indicator Gp | 1 |
2P-5481 | Deep Well Socket | 1 |
154-9521 | Spark Plug Seat Cleaner | 1 |
Illustration 12 | g00803420 |
(1) Gasket (2) O-ring seal (3) Adapter |
Use the 1F-0479 Wrench for removal and installation of the spark plug adapter. When you install the adapter, make sure that gasket (1) is in place. Apply liquid soap to O-ring seal (2) and the bore for the seal in the cylinder head. Apply 5P-3931 Anti-Seize Compound on the threads of the adapter and on the threads in the cylinder head. Tighten the adapter to a torque of
The 9U-6695 Spark Plug Firing Indicator Gp is an aid for determining ignition problems. Refer to the instructions that are included with the tool.
Bike Service Manual
The condition of the spark plug and the changes in engine load will vary the voltage that is needed to create a spark. A new spark plug in an engine at low idle requires approximately 3,000 to 6,000 V. At full load, 8,000 to 10,000 V are required. If the spark plug gap needs adjustment, more than 10,000 V are required. If the spark plug gap is too great, the requirement for voltage will increase. When the voltage for the spark plug is greater than 10,000 V, the engine will run rough.
Refer to the engine Operation and Maintenance Manual for instructions on inspection and installation of the spark plug.
Altronic Integral Transformer
Caterpillar G3304 Service Manuals
- Install new 108-6561 Gasket (5) on the spark plug.
The gasket is copper. Whenever the transformer is removed, always install a new gasket.
- Ensure that transformer (4) is clean and free from dirt and oil. Screw the transformer by hand onto the spark plug.
Tighten the transformer until the transformer bottoms out on the copper gasket. Tighten the transformer for an additional 1/8 of a turn (45 degrees). Do not overtighten the transformer.
- Inspect boot (3) for cleanliness and good condition. Install the boot.
- Tighten clamp (2).
- Inspect connector (1) for cleanliness and good condition. Reconnect the connector. Align the threads properly. For a correctly fastened connector, little thread or no thread is visible.
Illustration 13 | g00803356 |
(1) Connector (2) Clamp (3) Boot (4) Transformer (5) Gasket |
Adjustment of the Contact Points for the Gauges
The adjustment of the contact for the engine oil pressure gauge is correct when the engine is stopped at
Adjustment of the gauges is made with a small hex head wrench. Turn the adjustment screw on the gauge until the correct point is achieved.
Illustration 14 | g00675751 |
Water temperature gauge (1) Adjustment screw |
Illustration 15 | g00675777 |
Engine oil pressure gauge (1) Adjustment screw |
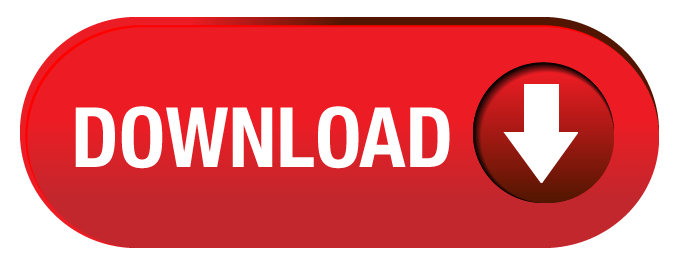